Yorulma kırılmasını gözlemlemek ve kırılma mekanizmasını analiz etmek için taramalı elektron mikroskobu kullanıldı; aynı zamanda, test çeliğinin dekarbürizasyonlu ve dekarbürizasyonsuz yorulma ömrünü karşılaştırmak ve dekarbürizasyonun test çeliğinin yorulma performansı üzerindeki etkisini analiz etmek için farklı sıcaklıklarda dekarbürize edilmiş numuneler üzerinde spin bükme yorulma testi yapıldı. Sonuçlar, ısıtma işleminde oksidasyon ve dekarbürizasyonun eş zamanlı varlığı nedeniyle, ikisi arasındaki etkileşimin, sıcaklığın büyümesiyle birlikte tamamen dekarbürize edilmiş katmanın kalınlığının artmasıyla sonuçlanan bir artış ve daha sonra azalma eğilimi gösterdiğini göstermektedir. Tamamen dekarbürize edilmiş katmanın kalınlığı 750 °C'de maksimum 120 μm değerine ulaşır ve tamamen dekarbürize edilmiş katmanın kalınlığı 850 °C'de minimum 20 μm değerine ulaşır ve test çeliğinin yorulma sınırı yaklaşık 760 MPa'dır ve test çeliğindeki yorulma çatlaklarının kaynağı esas olarak Al2O3 metalik olmayan kalıntılardır; dekarbürizasyon davranışı, test çeliğinin yorulma ömrünü büyük ölçüde azaltır, test çeliğinin yorulma performansını etkiler, dekarbürizasyon katmanı ne kadar kalınsa yorulma ömrü o kadar düşük olur. Dekarburizasyon katmanının test çeliğinin yorulma performansı üzerindeki etkisini azaltmak için test çeliğinin optimum ısıl işlem sıcaklığı 850°C'ye ayarlanmalıdır.
Dişli otomobilin önemli bir bileşenidirYüksek hızda çalışma nedeniyle, dişli yüzeyinin birbirine geçen kısmı yüksek mukavemete ve aşınma direncine sahip olmalı ve malzemeye yol açan çatlakları önlemek için diş kökünün sürekli tekrarlanan yük nedeniyle iyi bir bükülme yorulma performansına sahip olması gerekir. kırık. Araştırmalar, dekarbürizasyonun metal malzemelerin spin bükme yorulma performansını etkileyen önemli bir faktör olduğunu ve spin bükme yorulma performansının ürün kalitesinin önemli bir göstergesi olduğunu, dolayısıyla test malzemesinin dekarbürizasyon davranışının ve spin bükme yorulma performansının incelenmesi gerektiğini göstermektedir.
Bu yazıda, ısıl işlem fırınında 20CrMnTi dişli çeliği yüzey dekarbürizasyon testi, değişen yasanın test çeliği dekarbürizasyon katman derinliği üzerindeki farklı ısıtma sıcaklıklarını analiz eder; Test çeliği döner bükme yorulma testinde QBWP-6000J basit kiriş yorulma test makinesini kullanarak, test çeliği yorulma performansının belirlenmesi ve aynı zamanda gerçek üretimin iyileştirilmesi için dekarbürizasyonun test çeliğinin yorulma performansı üzerindeki etkisini analiz etmek Üretim sürecini, ürünlerin kalitesini artırın ve makul bir referans sağlayın. Test çeliği yorulma performansı, dönerek bükme yorulma test makinesi tarafından belirlenir.
1. Test malzemeleri ve yöntemleri
20CrMnTi dişli çeliği sağlayan bir ünite için test malzemesi, ana kimyasal bileşim Tablo 1'de gösterilmiştir. Dekarbürizasyon testi: test malzemesi Ф8 mm x 12 mm silindirik numuneye işlenir, yüzey lekesiz parlak olmalıdır. Isıl işlem fırını, numunenin içine 675 ° C, 700 ° C, 725 ° C, 750 ° C, 800 ° C, 850 ° C, 900 ° C, 950 ° C, 1.000 ° C'ye kadar ısıtıldı ve 1 saat bekletildi ve ardından oda sıcaklığına kadar havayla soğutuldu. Numunenin %4'lük nitrik asit alkol çözeltisi erozyonu ile sertleştirme, taşlama ve cilalama yoluyla ısıl işleminden sonra, test çeliği dekarbürizasyon katmanını gözlemlemek için metalurjik mikroskopi kullanılarak, farklı sıcaklıklarda dekarbürizasyon katmanının derinliği ölçülür. Spin bükme yorulma testi: iki grup spin bükme yorulma numunesinin işlenmesinin gerekliliklerine göre test malzemesi, birinci grup dekarbürizasyon testi yapmaz, ikinci grup farklı sıcaklıklarda dekarbürizasyon testi yapar. Döndürerek bükme yorulma test makinesini kullanarak, döndürerek bükme yorulma testi için iki test çeliği grubu, iki test çeliği grubunun yorulma sınırının belirlenmesi, iki test çeliği grubunun yorulma ömrünün karşılaştırılması, tarama kullanımı Elektron mikroskobu yorulma kırığı gözlemi, numunenin kırılma nedenlerini analiz etmek, test çeliğinin yorulma özelliklerinin dekarbürizasyonunun etkisini araştırmak.
Tablo 1 Test çeliğinin kimyasal bileşimi (kütle oranı) ağırlıkça %
Isıtma sıcaklığının dekarbürizasyona etkisi
Farklı ısıtma sıcaklıkları altında dekarbürizasyon organizasyonunun morfolojisi Şekil 1'de gösterilmektedir. Şekilden görülebileceği gibi, sıcaklık 675 °C olduğunda numune yüzeyinde dekarbürizasyon katmanı görülmez; sıcaklık 700 ° C'ye yükseldiğinde, ince ferrit dekarbürizasyon katmanı için numune yüzeyi dekarbürizasyon katmanı görünmeye başladı; sıcaklığın 725 °C'ye yükselmesiyle numune yüzeyi dekarbürizasyon katmanı kalınlığı önemli ölçüde arttı; 750 °C dekarbürizasyon tabakası kalınlığı maksimum değerine ulaşır, bu sırada ferrit tanesi daha berrak, kabadır; sıcaklık 800 ° C'ye yükseldiğinde, dekarburizasyon tabakasının kalınlığı önemli ölçüde azalmaya başladı, kalınlığı 750 ° C'nin yarısına düştü; sıcaklık 850 °C'ye yükselmeye devam ettiğinde ve dekarbürizasyon kalınlığı Şekil 1'de gösterildiğinde. 800 °C'de, tam dekarbürizasyon tabakası kalınlığı önemli ölçüde azalmaya başladı, kalınlığı yarıya indiğinde 750 °C'ye düştü; sıcaklık 850 ° C'ye ve üstüne yükselmeye devam ettiğinde, test çeliğinin tam dekarbürizasyon tabakası kalınlığı azalmaya devam eder, yarım dekarbürizasyon tabakası kalınlığı, tam dekarbürizasyon tabakası morfolojisinin tamamı kayboluncaya kadar kademeli olarak artmaya başlar, yarım dekarbürizasyon tabakası morfolojisi yavaş yavaş netleşir. Sıcaklık artışıyla birlikte tamamen karbonu giderilmiş tabakanın kalınlığının önce arttığı ve sonra azaldığı görülebilir; bu olgunun nedeni numunenin ısıtma işleminde aynı zamanda oksidasyon ve dekarbürizasyon davranışından kaynaklanmaktadır. dekarbürizasyon oranı, oksidasyon hızından daha hızlıdır ve dekarbürizasyon fenomeni ortaya çıkacaktır. Isıtmanın başlangıcında, tamamen karbonu giderilmiş katmanın kalınlığı, tamamen karbonu giderilmiş katmanın kalınlığı maksimum değere ulaşana kadar sıcaklık artışıyla birlikte kademeli olarak artar, bu sırada sıcaklığı yükseltmeye devam etmek için numune oksidasyon hızı, normalden daha hızlıdır. Tamamen dekarbürize edilmiş katmanın artışını engelleyen dekarbürizasyon oranı, düşüş eğilimine neden olur. 675 ~ 950 °C aralığında, 750 °C'de tamamen dekarbürize edilmiş tabakanın kalınlık değerinin en büyük olduğu ve 850 °C'de tamamen dekarbürize edilmiş tabakanın kalınlık değerinin en küçük olduğu görülebilir. bu nedenle test çeliğinin ısıtma sıcaklığının 850°C olması önerilir.
Şekil 1 1 saat boyunca farklı ısıtma sıcaklıklarında tutulan dekarbürize test çeliği katmanının histomorfolojisi
Yarı dekarbürize edilmiş katmanla karşılaştırıldığında, tamamen dekarbürize edilmiş katmanın kalınlığı malzeme özellikleri üzerinde daha ciddi bir olumsuz etkiye sahiptir; malzemenin mukavemetini, sertliğini, aşınma direncini ve yorulma sınırını azaltmak gibi mekanik özelliklerini büyük ölçüde azaltacaktır. vb. ve ayrıca kaynak kalitesini etkileyen çatlaklara karşı hassasiyeti arttırır. Bu nedenle, tamamen karbonsuzlaştırılmış katmanın kalınlığının kontrol edilmesi, ürün performansının iyileştirilmesi açısından büyük önem taşımaktadır. Şekil 2, tamamen karbonu giderilmiş katmanın kalınlığının sıcaklıkla değişim eğrisini gösterir; bu, tamamen karbonu giderilmiş katmanın kalınlığının değişimini daha açık bir şekilde gösterir. Tamamen dekarbürize edilmiş katmanın kalınlığının 700°C'de yalnızca yaklaşık 34μm olduğu şekilde görülebilir; Sıcaklık 725 °C'ye yükseldiğinde, tamamen karbonu giderilmiş katmanın kalınlığı önemli ölçüde 86 μm'ye yükselir; bu, 700 °C'de tamamen dekarbürize edilmiş katmanın kalınlığının iki katından fazladır; sıcaklık 750 °C'ye yükseltildiğinde, tamamen karbonu giderilmiş katmanın kalınlığı Sıcaklık 750°C'ye yükseldiğinde, tamamen dekarbürize edilmiş katmanın kalınlığı maksimum 120 μm değerine ulaşır; Sıcaklık artmaya devam ettikçe, tamamen karbonu giderilmiş katmanın kalınlığı keskin bir şekilde azalmaya başlar, 800°C'de 70 μm'ye ve ardından 850°C'de yaklaşık 20μm'lik minimum değere düşer.
Şekil 2 Farklı sıcaklıklarda tamamen karbonu giderilmiş tabakanın kalınlığı
Dönerek bükmede dekarbürizasyonun yorulma performansına etkisi
Dekarbürizasyonun yay çeliğinin yorulma özellikleri üzerindeki etkisini incelemek amacıyla iki grup dönerek bükme yorulma testi yapıldı; birinci grup dekarbürizasyon olmadan doğrudan yorulma testi, ikinci grup ise aynı streste dekarbürizasyon sonrası yorulma testiydi. seviyesinde (810 MPa) ve dekarburizasyon işlemi 1 saat boyunca 700-850 ° C'de tutuldu. İlk numune grubu, yay çeliğinin yorulma ömrünü gösteren Tablo 2'de gösterilmektedir.
Birinci grup numunelerin yorulma ömrü Tablo 2'de gösterilmektedir. Tablo 2'den görülebileceği gibi, dekarbürizasyon olmadan test çeliği 810 MPa'da yalnızca 107 döngüye tabi tutulmuş ve herhangi bir kırılma meydana gelmemiştir; gerilme seviyesi 830 MPa'yı aştığında bazı numuneler kırılmaya başladı; stres seviyesi 850 MPa'yı aştığında yorulma numunelerinin tümü kırıldı.
Tablo 2 Farklı stres seviyeleri altında yorulma ömrü (dekarburizasyon olmadan)
Yorulma sınırını belirlemek için, test çeliğinin yorulma sınırını belirlemek için grup yöntemi kullanılır ve verilerin istatistiksel analizinden sonra test çeliğinin yorulma sınırı yaklaşık 760 MPa'dır; Test çeliğinin farklı stresler altındaki yorulma ömrünü karakterize etmek için Şekil 3'te gösterildiği gibi SN eğrisi çizilir. Şekil 3'ten görülebileceği gibi, farklı stres seviyeleri farklı yorulma ömrüne karşılık gelir; 107 için döngü sayısına karşılık gelir; bu, bu koşullar altındaki numunenin durumdan geçtiği anlamına gelir; karşılık gelen gerilim değeri, yorulma mukavemeti değeri, yani 760 MPa olarak yaklaşık olarak tahmin edilebilir. Malzemenin yorulma ömrünün belirlenmesinde önemli olan S – N eğrisinin önemli bir referans değerine sahip olduğu görülmektedir.
Şekil 3 Deneysel çelik döner eğilme yorulma testinin SN eğrisi
İkinci grup numunelerin yorulma ömrü Tablo 3'te gösterilmektedir. Tablo 3'ten görülebileceği gibi, test çeliği farklı sıcaklıklarda karbonsuzlaştırıldıktan sonra çevrim sayısı açıkça azalır ve bunlar 107'den fazladır ve hepsi yorulma numuneleri kırılır ve yorulma ömrü büyük ölçüde azalır. Yukarıdaki dekarbürize edilmiş katman kalınlığı ile birlikte sıcaklık değişim eğrisi görülebildiğinde, 750 ⁰ dekarbürlenmiş katman kalınlığı en büyük olup yorulma ömrünün en düşük değerine karşılık gelir. 850 °C dekarbürize tabaka kalınlığı en küçüktür, yorulma ömrü değerine karşılık gelen nispeten yüksektir. Dekarbürizasyon davranışının malzemenin yorulma performansını büyük ölçüde azalttığı ve dekarbürize tabaka ne kadar kalınsa yorulma ömrünün o kadar düşük olduğu görülebilir.
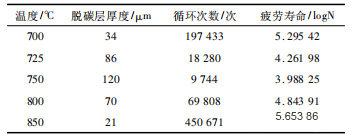
Tablo 3 Farklı dekarburizasyon sıcaklıklarında yorulma ömrü (560 MPa)
Numunenin yorulma kırılma morfolojisi, Şekil 4'te gösterildiği gibi taramalı elektron mikroskobu ile gözlemlenmiştir. Şekil 4(a), çatlak kaynak alanı için, kaynağı bulmak için yorulma yayına göre, şekil açıkça yorulma yayı görülebilir. Yorulma, görülebilir, "balık gözü" metalik olmayan kalıntılar için çatlak kaynağı, yorulma çatlaklarına neden olan stres konsantrasyonuna neden olan kalıntılar; Çatlak genişleme alanı morfolojisi için Şekil 4(b), belirgin yorulma şeritleri görülebilmektedir, nehir benzeri bir dağılımdır, yarı ayrışmalı kırılmaya aittir, çatlaklar genişleyerek sonunda kırılmaya yol açmaktadır. Şekil 4(b) çatlak genişleme alanının morfolojisini göstermektedir; yarı ayrışmalı kırılmaya ait nehir benzeri dağılım biçiminde ve çatlakların sürekli genişlemesiyle sonuçta kırılmaya yol açan bariz yorulma çizgileri görülebilir. .
Yorulma kırılma analizi
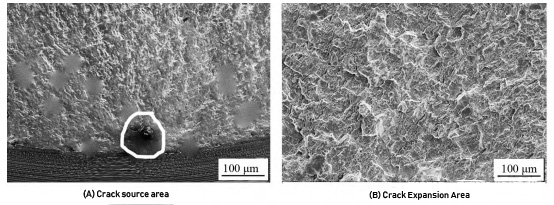
Şekil 4 Deneysel çeliğin yorulma kırılma yüzeyinin SEM morfolojisi
Şekil 4'teki kapanımların tipini belirlemek için enerji spektrumu kompozisyon analizi gerçekleştirilmiş ve sonuçlar Şekil 5'te gösterilmiştir. Metalik olmayan kapanımların çoğunlukla Al2O3 kapanımları olduğu görülebilmektedir. inklüzyon çatlamalarından kaynaklanan çatlakların ana kaynağıdır.
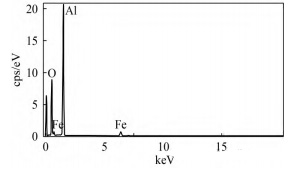
Şekil 5 Metalik Olmayan Kalıntıların Enerji Spektroskopisi
Sonuçlandırmak
(1) Isıtma sıcaklığının 850 °C'ye konumlandırılması, yorulma performansı üzerindeki etkiyi azaltmak için karbonu giderilmiş katmanın kalınlığını en aza indirecektir.
(2) Test çeliğinin dönerek bükülmesinin yorulma sınırı 760 MPa'dır.
(3) Metalik olmayan kalıntılarda, özellikle Al2O3 karışımında test çeliği çatlaması.
(4) dekarbürizasyon, test çeliğinin yorulma ömrünü ciddi şekilde azaltır, dekarbürizasyon tabakası ne kadar kalınsa yorulma ömrü o kadar düşük olur.
Gönderim zamanı: Haz-21-2024